Retrofit in intralogistics:
advantages through the implementation of brownfield solutions
Retrofit solutions offer operators of existing intralogistics systems new opportunities to increase performance without having to completely dismantle the old systems.
Extending existing plant systems
Why carry out a retrofit?
The demands on existing systems have risen considerably due to the increasing volume. This has an impact on all sectors of the economy and in the fast-moving world of intralogistics in particular, efficiency is paramount. Companies must continually look for ways to optimize their existing systems in order to remain competitive. One proven method of achieving this goal is the so-called retrofit. But why should you even consider a retrofit and when is it worthwhile?
A retrofit offers a cost-effective way of bringing older installations and systems up to the latest state of the art without having to completely replace the entire infrastructure. Existing systems are often still functional, but no longer state of the art. There are solutions with higher productivity promises for many technical solutions. By modernizing them, they can be equipped with new functions and improved performance features to increase efficiency and optimize operation. In addition, a retrofit enables the integration of new technologies such as automated control systems, sensor technology and data analysis to further optimize processes and strengthen competitiveness.
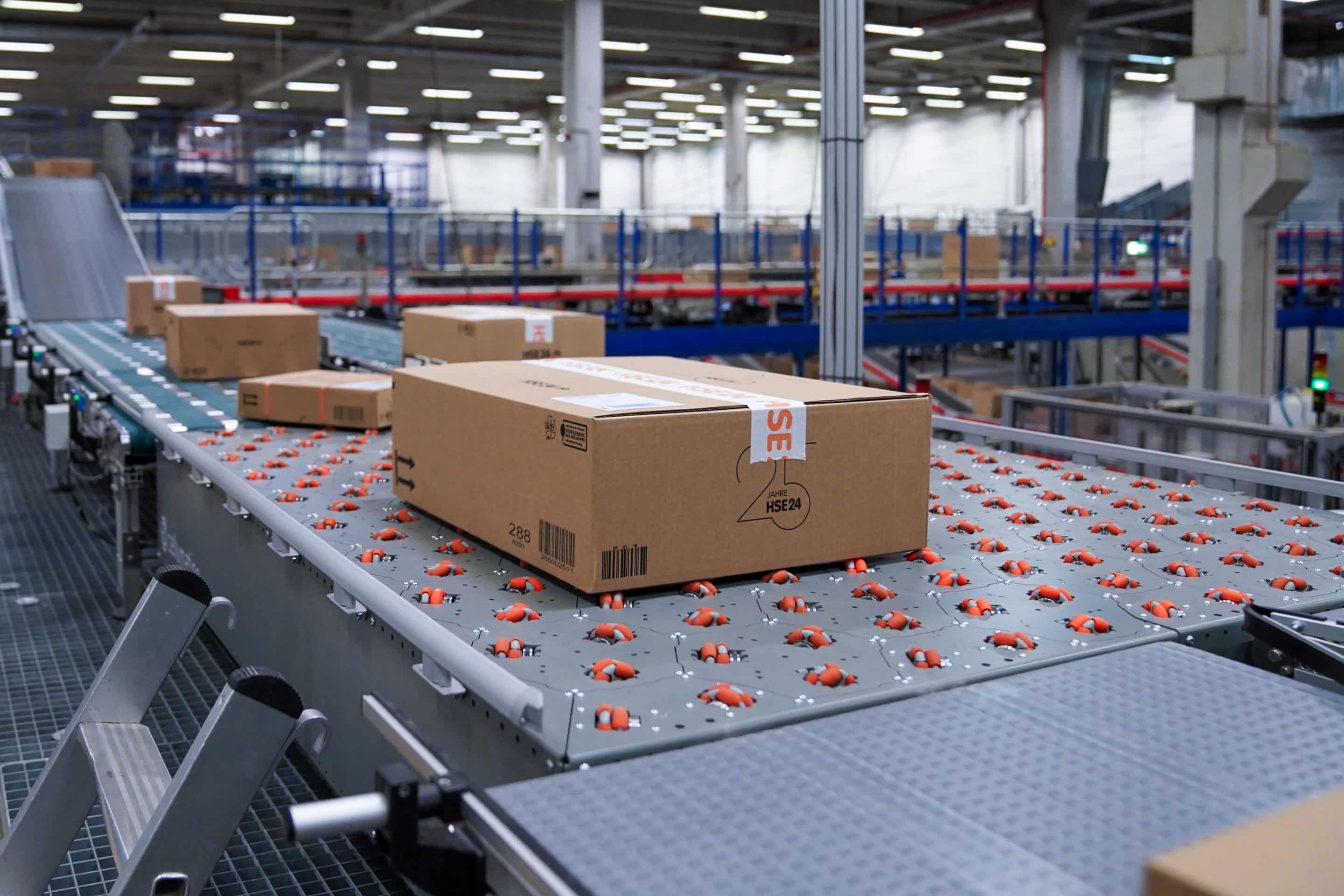
Checklist: What to look out for when carrying out a retrofit in the existing system.
- Compatibility:
Ensure that the new components and technologies are compatible with existing systems and equipment. Smooth integration is crucial to minimize disruptions and downtime.
- Flexibility:
Take into account the flexibility of the new solutions to be used on existing surfaces. Adaptable technologies, such as celluveyor technology, not only make implementation easier, but also enable future expansions and adaptations.
- Interface communication:
Simple and efficient communication between the various systems is of great importance. Make sure that the interfaces function smoothly and that data can be exchanged seamlessly. The easiest way to do this is through industry standards.
- Safety:
Keep an eye on safety aspects, especially when new automated systems are introduced. Ensure that safety standards are adhered to and that employees and operating equipment are protected from potential risks. Involve your occupational safety experts in your plans as early as possible so that they can accompany the process parallel to the planning and go live with the system immediately.
- Education and training:
Invest in training measures for your employees to ensure that they are familiar with the new systems and technologies. Well-trained employees make a significant contribution to smooth operation and increased efficiency.
Optimize existing systems
When is a retrofit worth it?
The decision for a retrofit depends on various factors. Firstly, the age of the existing systems plays a role. The older they are, the more likely it is that they no longer meet current requirements and standards. In such cases, a retrofit offers a cost-effective alternative to a new build. In addition, changes in operational requirements, such as increased demand or new production processes, can prove to be the driving force behind a retrofit project.
Another important aspect is the cost-effectiveness of the retrofit compared to a new build. A retrofit is often significantly more cost-effective and time-saving than the construction of a new plant. By using existing resources and infrastructure, companies can not only save on investment costs, but also minimize downtime and quickly restore productivity.
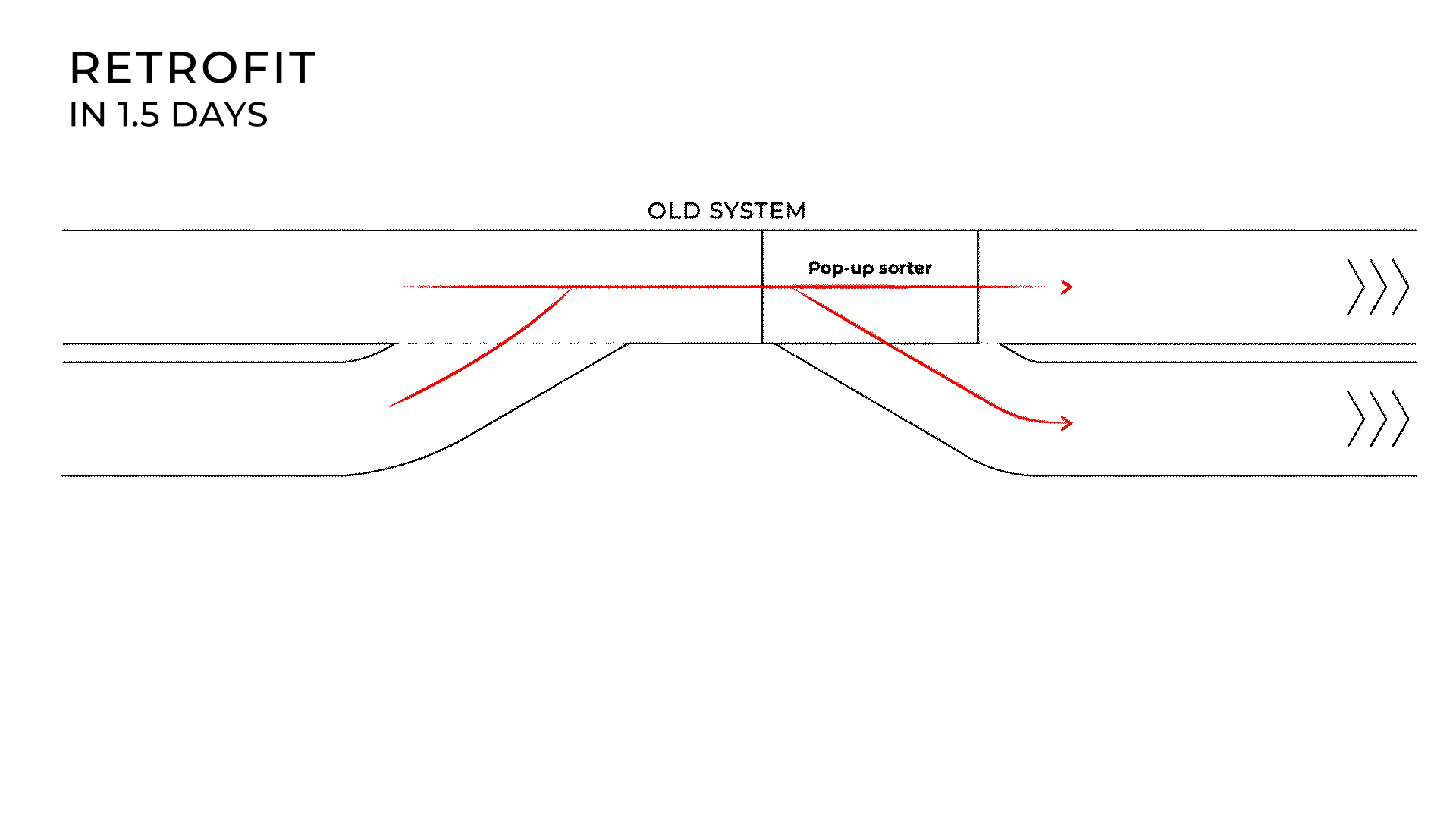
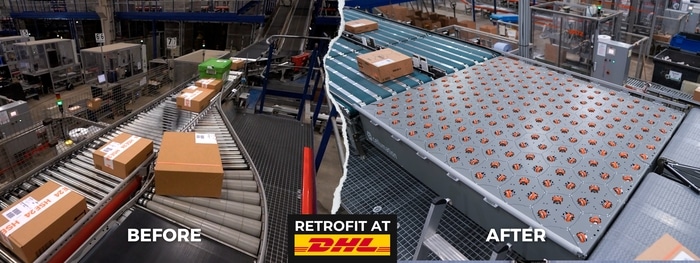
To determine whether a retrofit is worthwhile, companies should carefully examine the following factors:
1. Condition of existing systems:
Examine the current condition of the existing systems and assess their performance and reliability. Determine whether they still meet the operational requirements or whether they need to be modernized.
2. Labor shortage and automation potential:
Consider the current labor shortage in the industry and the potential of automation to replace skilled workers and avoid work stoppages. By integrating automated systems, companies can reduce their reliance on human labor while ensuring the efficiency and continuity of their operations. Therefore, consider automation as a way to bridge recruitment bottlenecks and increase productivity in the long term.
3. Age of the plants:
Consider the age of the systems, as older systems tend to be more prone to breakdowns and more inefficient in terms of energy consumption and performance. A retrofit can be a cost-effective alternative to a new build.
4. Operational requirements and objectives:
Analyze the company’s current operational requirements and long-term goals. Check whether the existing systems can meet these requirements or whether a retrofit is necessary to increase efficiency and improve competitiveness.
5. Economic efficiency:
Carry out a comprehensive cost-benefit analysis to assess the cost-effectiveness of a retrofit. Take into account not only the investment costs for the retrofit project, but also potential savings through improved efficiency, lower maintenance costs and a longer service life of the systems.
6. Technological development:
Keep informed of the latest technological developments and innovations in the industry. Check whether new technologies and solutions are available that can improve system performance and optimize operations.
Why automation in intralogistics helps you do more with fewer hands
Digression
Why automation in intralogistics helps you do more with fewer hands
Automation is playing an increasingly important role in intralogistics as companies look for ways to optimize their operations and make them more efficient. A key aspect of this is the ability to do more with fewer hands. By using automated systems and robotics, companies can streamline their production and warehouse processes while reducing their reliance on human labor.
One exciting solution for brownfield automation is the celluveyor. This innovative conveyor belt system offers a variety of benefits for companies looking to modernize their existing facilities. The celluveyor is characterized by its flexibility and adaptability and enables efficient material flow control in various application areas. By integrating celluveyor systems, companies can automate their production processes and significantly increase the efficiency of their intralogistics.
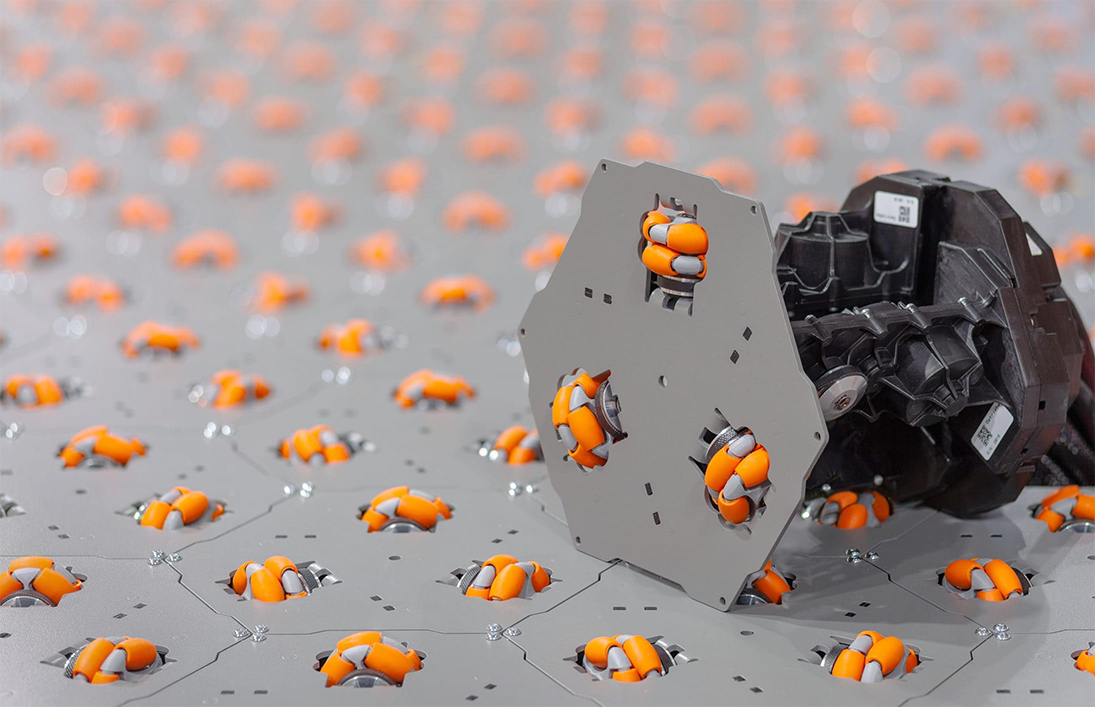
Retrofit use cases
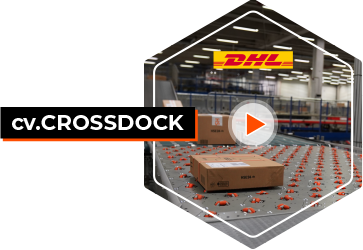
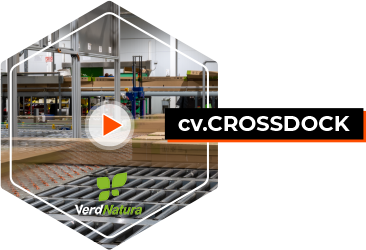
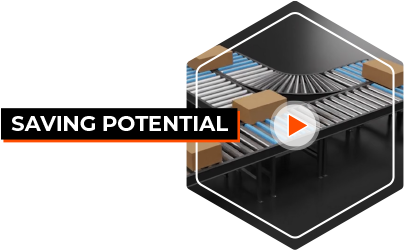
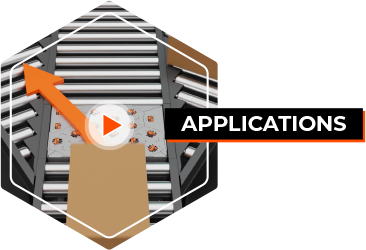
Advantages of implementing Brownfield solutions
Implementing a retrofit as part of brownfield solutions offers additional benefits for intralogistics companies. In contrast to greenfield projects, where completely new facilities are built on a greenfield site, a brownfield retrofit enables the optimization of existing sites and facilities. This allows companies to maximize their investments while maintaining operations.
A key advantage of brownfield retrofits is the reduction of risks and uncertainties compared to new construction projects. As an existing infrastructure is already in place, the adjustments and integrations are generally less complex and involve fewer risks. In addition, companies can benefit from shorter planning and implementation times, as the foundations are already in place and do not have to be created from scratch.
Another compelling argument for increased automation is the improvement in operational efficiency and competitiveness.
Through the targeted use of automated systems, companies can optimize their production processes and improve the quality of their products and services at the same time. Automation enables tasks to be carried out precisely and reliably, which leads to a reduction in errors and rejects. In addition, companies can also increase their production speed and respond more flexibly to customer requirements thanks to automation technologies. Increased automation therefore not only offers the opportunity to reduce costs, but also to increase productivity and improve customer loyalty.
Overall, a retrofit in intralogistics, especially in the context of brownfield solutions, offers a wide range of benefits for companies. From cost efficiency and risk minimization to sustainability, companies can optimize their existing systems and strengthen their competitiveness at the same time.
Let’s talk!
Let’s talk about how we can achieve the highest performance in your material handling system with our powerful celluveyor technology.

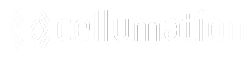
Tel. +49 (0) 421 331135 0
Fax +49 (0) 421 33 11 35 99
Mail info@cellumation.com
Kleiner Ort 7
28357 Bremen
Germany
Legal notice & Jobs